試作板金加工 加工技術情報
板金加工の分類
世の中には多くの金属製品が漆れている。我々の日々の生活を眺めただけでも、冷蔵庫、洗濯機、ストーブ、スチール家具、自動販売機、あるいはファクシミリ、コピー機などの事務機器、エレベーター 等々、数えきれない程である。
そして、これらの大半が板金加工という工程を経て製品となっている。 板金加工とは、平らな板を切ったり、穴あけしたり、曲げたり、溶接したりして指定の形状を作りあげる加工を総称するものだが、その加工方式および加工製品は多岐にわたっている。その分類の仕方もいろいろとあるが、ここでは、技能検定の分類並びに世の中での通称を記して、整理する。 技能検定では大きくは建築板金と工場板金の二つに分類され、これらがさらに小分類されている。
これから深く言及しようとしているのは、工場板金の中の「機械板金作業Jと「数値制御タレットパンチプレス板金作業」の2作業職種についてであって、この業界では一般に、機械板金とか精密板金とかと呼ばれている分野である。 この2作業職種は共に板金加工機械を駆使しての加工であり、残る4作業は手加工が主体である。そこで業界の中では、機械板金(精密板金)、手板金(タタキ板金)という分け方をすることもある。 機械板金(精密板金)とは、高度な板金加工機械を駆使して精密な製品を作りあげることから、いつとはなしによばれるようになった名称である。
なお、精密板金の精密とは、かつて手板金(タタキ板金)に比較しての精密さが強調されての呼び名だったのだが、最近では、機械板金の中でも特に高精度加工(例えば加工精度±0 1mm以下)のものを指す場合も多くなった。 手板金、タタキ板金という呼び方は、手作業主体で、金属板をトントン叩いて加工するからである。加工精度的には手作業の限界もあるので、±0.5~2 mm程度である。 また、工場板金の中の打出し板金を自動車板金という呼び方をすることもある。建築板金を屋根板金ということもある。 トタン、亜鉛鉄板などの屋根材を加工、施行するからである。いずれの呼び方も、加工の実態を言い表していると言える。
板金加工機械の変遷
現在の板金加工分野の分類は以上の通りであるがこの業界に高度を板金加工機械が登場し始めたのは昭和30年代後半になってからである。 その登場、そして普及と共に、板金加工機械の高性能・高精度が注目され、徐々に多業種の多製品が板金加工されるようになったものである。 また、その当時から我が国経済も上昇カーブを描き始め、それにつれて板金加工機械を導入する業種も急、速拡大したものとも言える。殊に昭和39年の東京オリンピックを契機としての家庭電気製品の普及 は、板金加工の必然性・重要性を確固としたものにした。 従来の板金加工というものを根底から覆し、現代の板金加工を形作ったのは、実に、高性能,高精度板金加工機械の登場にほかならないのである。 その機械とは、シャーリングマシン、NCタレットパンチプレス、油圧式プレスブレーキである。
シャーリングマシンについて
ますシャーリングマシンは、昭和40年代のはじめ、切断寸法を設定するバヽックゲージ(後定規)がデデタル表示式の電動式バックゲージとなったことにより、この業界に大きな変化をもたらした。 それまで高精度切断を行う際には、切断―→測定―→切断―→測定を繰り返さねばならなかったが、この電動式パッケージの登場は、切断の技術、方式というものを一挙に数歩、前進させた。 "板金加工を0.1mm単位で"という概念が徐々に形成され始めた端緒にもなっている。
NCタレットパンチプレスについて
今日の板金加工の大発展は、何と言っても、NC(数千直制御)タレットパンチプレスが開発されたことである。 この開発・登場によって、従来はプレス加工の領域であった製品の加工が、板金加工領域に入り込んで来たのである。周知のようにNCタレットパンチプレスは、標準化された多くの金型を組み合 せることによって加工ができるのだが、これは、プレス加工が、加工品が変わるたびに高価な金型を作るということと比較して、大革新と呼ぶにふさわしいものがあった。 加工速度の面で見ても、飛躍的だった。標準金型の組み合せが安直にでき、加工速度も速いという利便性は、どんな少量生産も可能ということでもあり、多種少量生産から多量生産の領域に至るまで、板金加工の分野を拡大させるものであった。 このNCタレットパンチプレスの優位性は現在においても変わらず、板金FMSの核の役割を呆たす機械となっている。 なお、我が国におけるこの機械の開発・普及は、昭和40年代半ばからだった。
油圧式プレスブレーキについて
今日の板金加工の大発展は、何と言っても、NC(数千直制御)タレットパンチプレスが開発されたことである。 この開発・登場によって、従来はプレス加工の領域であった製品の加工が、板金加工領域に入り込んで来たのである。周知のようにNCタレットパンチプレスは、標準化された多くの金型を組み合 せることによって加工ができるのだが、これは、プレス加工が、加工品が変わるたびに高価な金型を作るということと比較して、大革新と呼ぶにふさわしいものがあった。 加工速度の面で見ても、飛躍的だった。標準金型の組み合せが安直にでき、加工速度も速いという利便性は、どんな少量生産も可能ということでもあり、多種少量生産から多量生産の領域に至るまで、板金加工の分野を拡大させるものであった。 このNCタレットパンチプレスの優位性は現在においても変わらず、板金FMSの核の役割を呆たす機械となっている。 なお、我が国におけるこの機械の開発・普及は、昭和40年代半ばからだった。
以上が『板金革命の旗手』こと呼ぶべき3機1放の概要である。それ以後の板金加工の発展は、我が国経済の成長と期を―にするものだが、それはとりもなおさず、産業界の需要に即した機械だったからである。
板金製品の種類
現代において、板金加工を必要とする業種、製品は以下のように多岐にわたっている。
- 家電製品
- 自動販売機、キャッシュティスペンサー、両替機など
- 配電盤
- 通信機器
- 建築、製罐
- 厨房機器、ショウケース
- 家具
- 事務機器
- 化学機械、食品機械
- 工作機械
- コンピューター関係
- 航空機、原子炉
- 自動車、農機
などである。
高性能。高精度の板金加工機械が普及したことが、板金加工の発展に連なったことは述べた通りだが、このように我が国産業の大半の分野を市場とするとは過去に考えられないことであった。
板金加工の工程と加工特性
板金加工が多業種、多製品にわたる一方で、その加工工程も非常に広範である。
加工工程は、主につぎのようなものである。
- せん断力日工(シャーリング)
- 打抜き加工(パンチング)
- 曲げ加工(ベンディング)
- 溶接加工、溶断加工
- 表面処理
- 組立て
などである。
そして、以上のそれぞれの工程ごとに異なった加工機械が稼働し、板金製品が生産されているのであるが、それぞれの機械の操作にも異なった技術が要求されるし、 また、加工の材質が変わるだけでその操作・調整技術にも異なったものが要求される[―見しただけでは、簡単に思える機械操作も、実は豊富な知識、技能、経験がなければ、思うに任せない)手加工の時代には、す丈術者自身のウテ、カン、経験による熟練技能が絶対的に要求されたが、現代の板金機械加工の時代にあっては、―見しただけでは、簡単に思える機械操作も、実は豊富な知識、技能、経験がなければ、思うに任せない、手加工の時代には、す丈術者自身のウテ、カン、経験による熟練技能が絶対的に要求されたが、現代の板金機械加工の時代にあっては、
高精度の板金加工機械の操作技術、機械特有のクセを上手に使いこなす技能、そして、材料を始めとした板金加工全般にわたっての豊富な知識が要求されるとも言える。
熟練が必要とされるのは、今も昔も変わらない。また、板金加工の特性として第一に掲げられることは、多種少量生産ということであろう。短納期、多形状(多様製品)、低コストということも顕著である。
実際、加工数量が1個~数個ということも日常、当然のこととなっているし、受注の翌日納品、コスト低減要求ということも然りである。商品の多様化と商品寿命の低下がこれに拍車をかけている。
板金加工機械は、こうした要求を満たす便利な機械だが、同時に、自社の加工内容に見合った生産設備の選択、そして稼働体制の構築も大切なこととなっている。過去の「カンと経験」による品質管理から脱却し、数値・統計などによる科学的管理が絶対不可欠である。
板金加工の基本的知識
以上、板金加工を概観してきたが、さらに基本的な知識、用話についても触れる。
シャー角 rake angel |
シャーリングまたはパンチングにおける、下刃と上刃とのなす角度のことで、レーキ角ともいう。シャー角はシャーリング、パンチングにおいて、切断荷重を小さくするため設ける方法の1つである。シャー角を設けることによって切断荷重を少なくすることができるが、一方シャー角を大きくすると、切断された製品の変形、つまリボウ、ツイスト等が大きくなるため、一般的にはシャー角が小さい方が製品精度はよくなる。シャーリングにおいては一定の機械能力で薄板から厚板まで切断可能とするためシャー角可変機構を取り入れて製品を最適の状態で切断できるようにしたものもある6アマグのHタイプシャーリングが代表例。 |
クリアランス clearance |
シャーの上刃と下刃をかみ合せたときの両者のすきまおよび、パンチプレスのパンチとダイをかみ合せたときの両者のすきまをいう。せん断面は図のような形状になるが、クリアランスの大小により、この形状は微妙に変化し、これがせん断精度に非常に大きな影響を与えるので、最適なせん断面を得るようにクリアランスを設定する。 |
せん断力 shearing force |
材料のごく接近した点に、材料の直角方向に逆向きの平行力が加わるときの外力。 |
せん断応力 shearing stress |
材料にせん断力が作用すると、その力に釣り合うため材料内部にその断面にそって反対向きで同量の抵抗力が生じる。これをせん断力といい、単位面積についてのせん断内力の大きさをせん断応力という。 |
せん断強さ(抵抗) shearing strength |
材料がせん断されるとき、そのせん断過程におけるせん断荷重の最大値を材料の切口総面積で割った値。つまり切リロ単位面積当りの見かけの最大せん断力。せん断強さは材料の種類、圧廷条件、熱処理の有無などによって異なる。一般に使われている値を示すと表のようになり、延性材料では引張り強さの約60~80%くらいである。 |
せん断面の形状 | a: せん断面: 大きなせん断ひずみを受けた面で、刃先面でこすられたバニッシュ加工の光沢をもっている。 b: 破断面: クラックを生じ、破断した部分に結晶粒面が出現し、微刀ヽな凹凸がはなはだしい。 C: だれ: 切り刃が食い込んだ際、圧下した自由表面であり、 クリアランスの増大にともなって増大する。 d: かえり: 切れ味のよい刃であればあまり発生しない。 また、クリアランスが板厚の20%くらいまでは変化しないが、これを越すとかえりは急激に大きくなる。また過小なクリアランスの場合は、せん断面が板厚全体に広がり、かえりも大きくなる。従って適正なクリアランスの範囲の刃先が鋭利であれば、だれとクリアランスは無関係と考えてよい。かえりはせん断過程において必ず現れるもので、軟質材の場合では最良の条件でも板厚の1~ 2%程度は止むをえない。刃先の摩耗に従ってかえりは増大する。またクリアランスの増大にともなって破断面の傾きは大きくなる。また一般にもろい材料では、だれとせん断は小さく、切り口の大部分は破断面となる。 |
キヤンパー camber |
シャーリングによって切断された帯板材を平面上に置き、ストレートエッジ(定規)等に突き当てた場合に、ストレートエッジの面(直線)に対して、切断線がわん曲した状態をいう。キャンバーは、材料の内部応力や、シャーの刃の調整不良などによっておこり、刃の傾斜角(レーキ角)は、ほとんど影響ないと考えてよい。キャンバーの原因は機械側にあると判断される場合が多い。しかし,アルミ板を切断してみてキャンバーが出なければ、機械は正常であると判断できる。一般に、キャンバーの量は板材の材質(均質性、不純物の度合)による。 |
ねじれ twist |
シャーリングにおいて、せん断加工を行ったときにおこる、ねじれの状態。ツイストともいう。1m単位で一端を基準として角度で表す。レーキ角により異なり、レーキ角が大きくなければツイストは大きくなり、レーキ角が小さくなればツイストは小さくなる。また、切断幅が小さくなればツイストは大きくなる。 |
そり bow |
金属を板金機械で加工した時に生じる曲がりのこと。たとえば素材をシャーリングマシンなどのせん断機で切断した場合、切断方向に沿って生じる曲がり。シャーで切断した材料の精度は、寸法精度、切断面精度および変形精度に大別される。変形精度はさらに、 そり、ねじれ(ツイスト)キャンバーに分類され、いずれも絶対量が小さい方が好ましい。そりとねじれは密接な関係があり、両者が単独で生じることはまれである。そりの発生およびその量に対する最大の要因はシャー角(上刃と下刃のなす角度)で、シャー角を刀ヽさくすることによりそりは減少する。また、〔切断幅/板厚〕を大きくすることによってもそりは減少する。シャー角を小さくできない場合や切断幅の小さい場合には、切断過程で素材を常に上刃に押さえつける(逆押え装置)ことにより、そりの発生をある程度抑えることができる。 |
切断長さ cutting length |
シャーリング作業における製品寸法の呼び方。バックゲージ方向の寸法を切断幅といい、シャーブレードの長手方向の寸法を切断長さという。 |
切断幅 cuttins width |
シャーリング作業における製品寸法の呼び方。刃面よリバックゲージ突当で面までの寸法をいう。 |
打抜き加工 blankins |
材料を2つ以上に分離する作業の中で、 もっとも多く利用されているせん断加工の一種であり、板材から必要な形状の部品を外形抜きする加工のことをいう。外形抜き、穴あけを総称して打抜き加工と呼んでいるが、一般に、外形抜き加工は、抜かれた部品が目的であり、穴あけ加工は、穴をあけることが目的であるため、穴あけと区別して使われている。 |
絞り加工 drawing |
平板から、継ぎ目のない中空容器を作る加工をいう。この加工法には、ハンマー等でたたいて容器の形を作る手加工、ブレス機械に金型を取り付け、ダイ(雌型)にパンチl雄型)を押し込んで形状を作るプレス加工、掟盤によく似た機械く回転する材料にへらを押し付けて形状を作るスピニング加工の3つの加工法がある。普通、絞り加工という場合、プレス機械による加工をいう。プレスによる絞り加工は図に示すように、あらかじめ製品のでき上がり寸法に合わせた素材(ブランク)をオ反押えで押さえながら、パンチを下降させて、形状を作る加工法である。絞り加工の種類としては、一般的な絞り、再絞り、逆絞り、張出し、 しごきの5つがある。 |
絞り比、紋り率 drawins ratio、drawins rate |
絞り比とは円筒容器を絞る場合、円板ブランク直径対絞り後の円筒径の値をいう。この逆数を絞り率という。絞り加工を行う場合、絞り比は重要な値である。絞り比の値が材質によって一定の範囲内になるように、1段絞り、2段絞り、または3段絞りと工程を分ける目安にする。塑性加工のプレスによる絞り加工において利用される。 |
曲げ加工 bendins |
鋼板などを折り曲げてV宇形、U字形、L字形などの断面形状にすることをいう。曲げ加工には、プレス機械やプレスブレーキを使う方法の他、折曲げ機布成およびベンディングロールなどがある。V曲げ加工の場合、図4に示すように、V形のパンチと同形状の浦のあるダイとの間で材料を強く押しつけて加工するのが一般的であるが、キズを嫌う製品などで1よ、ウレタングイを用いることもある。 |
最小曲げ半径 minimun bendins radius |
板物等の曲け加工において、害」れをおこさずに曲げられる最小の内Rのこと。材質、板厚、圧延方向、端面の仕上げ状態等により決定される。普通鋼材では、圧延方向に平行に曲げる場合と、圧廷方向と直角に曲げる場合とでは、後者の方が曲げ割れが生じにくいので、最小曲げ加工においては、材料の圧廷方向が指示される場合があるので注意しなければならない。 |
中立面 | 板材を曲げると板の外側は引っ張られて仲しへ、内側は圧縮されて縮む。伸びも縮みも板の表面が最も大きく、板の中心方向に行くに従って小さくなり、ある面(立体的に考える場合は面、板の断面で考えるときは線)で0となる。(伸びも縮みもしない)この面を中立面という。このため、曲げ加工の板取り寸法はこの中立面で計算する。 |
スプリングパック spring back |
折曲げ作業(とくにエアベンディング)において、製品角度が、加圧時の角度より大きくなる現象のこと。スプリングバック量は、ワークの材質、板厚、内側曲げ半径などによって変化する。一般に、材料が硬いものほど、また(内側曲げ半径)、(板厚)の比が大きいものほど、スフリングバック量は大きい。エアベンティングでは、あらかじめこのスプリングバックを見込んで、余分に曲げてやる必要がある(オーハーフォーミング)。コイニング曲げは、このスプリングハックを殺して、精度のよい曲げを行おうとするものである。 |
設計開発における試作検証について
試作とは、主として量産時における製品のシミュレーションを目的として行われます。想定される問題を量産前の段階で洗い出し、検証を行うために試作品を製作します。デザイン確認用の試作品ももちろんありますが、試作、特に量産前段階で行われる量産試作は、製品の製造工程を考慮した上での試作品設計・製作が必要です。具体的に、組み立てて形状や精度等を確認したいということであれば、検証に必要な部分以外は簡略化することで、短納期化、コストダウン等を図ることができます。
生産工程の戦略
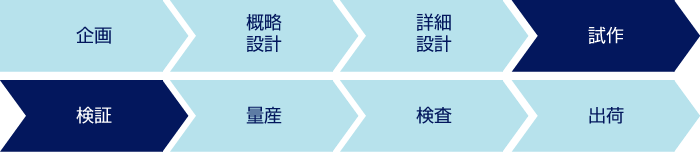
試作板金加工とは
通常の板金部品は量産を前提としたものが中心になりますが、"試作"板金加工では上記で触れたように目的が、量産を見据えた際の製品のデバッグが目的となります。特に板金部品の量産となると、金型を製作するケースが多くなり、試作の段階でどれだけ問題や課題を抽出して対処することが出来るかどうかということが、製品の品質やコストに大きく影響してきます。
一般には量産前試作と言われる段階ですが、板金部品においては金型製作のための検証が多くを占めます。試作板金部品のデバッグを実施後、設計修正によりもう一度部品がOKかどうかを確認し、金型の試作、金型の検証、と生産工程が進んで行きます。
また金型が製作され、生産ラインが立ち上がった後の組立て時にトラブル等が発生する場合は、再度試作品を作り、問題の洗い出しを行うケースも多く存在します。試作時の検証の質の差によって、量産時の製品品質やコストに差が生じます。
設計者にとって加工技術の知識は必須
設計者にとって、実際に部品がどのように加工されて製造されているのかを知っておくことは極めて重要な事項になります。部品メーカーがどういった機械を用いて、部品の量産を行っているのかということを知らなければ、機械の構造上加工できないような形状の設計をしてしまったり、また加工できても特殊な工程が必要になるために、コストが高くついてしまう設計をしてしまう可能性があります。
一般に、「部品コストの80%は設計段階で決まる」と言われますが、設計者には設計した部品がどのように製造されるのか、という点を理解した上での設計が求められます。
試作板金加工技術の知識
板金加工は1枚の平板から、「抜き」や「曲げ」によって3次元形状を作り出していきます。設計にあたっては、1枚の平面以外何もない状態から形状を作っていくため、設計のレベルとして高い技術が求められます。また部品メーカーの選定の際にも、加工技術を知っているかどうかということは重要なポイントとなります。板金加工は、見積もりも部品メーカーによって異なるケースが多くなります。その理由は、その会社それぞれの加工の進め方が異なるためなのですが、金属の削り出しのような加工方法と比較すると、板金加工は加工工程の自由度が大きいため、各社で技術や設備、段取りの仕方によって見積もりに大きな差が出てきやすい加工方法であると言えます。
試作板金加工の原理
板金加工における、加工の原理は3つにまとめることができます。すなわち、「打ち抜き」、「曲げ」、「絞り」の3つです。
この3つに、場合によって溶接やカシメといった加工が加わり板金部品が作られます。